A specialty steel manufacturing plant in India operated three centrifugal compressors with a combined capacity of 14,700 CFM. Each of these compressors was equipped with an orifice plate differential pressure flow sensor to measure the compressor output delivery, and the measured flow values were integrated into the compressor’s display panel. Together, the compressors consumed nearly 75,000 kWh per day. Refrigerant compressors were used to dry the air to a dew point of 3°C.
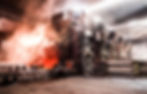
Reasons to Measure Your Compressed Air System
Compressed air isn’t as expensive as its mismanagement can make it to be. In a compressor’s life cycle cost, more than 85% of the costs are spent on its energy, whereas the capital and maintenance costs constitute the remaining 15%. Surprisingly, during a new system purchase, the focus is always on the capital costs with only theoretical considerations of the specific energy consumption. Specific energy consumption is a term used to define the amount of power a compressor consumes to deliver an output unit of compressed air. While most of the end users measure the compressor’s power consumption, the compressor's output flow remains unmeasured, leading to factual errors in their assumptions about their compressor’s specific energy consumption. The ambient conditions, coupled with the inefficiency and tolerance factors that are built into a compressor, can take a toll on its energy consumption and at times may increase the specific energy consumption even up to 30% of the compressor’s claimed efficiency. Hence, consistent monitoring of a compressor’s power consumption and discharge flow will form a key to maintaining the supply side efficiency. Further, a well-designed system should define the key performance indicators like flow, power, pressure, and dew point and should be measured at the right locations to understand the overall system dynamics as shown in the figure.
When the supply side of the system is not properly aligned with the demand side, it leads to an overcompensation of system pressures, resulting in increased artificial demand and associated issues such as:
• Increased air demand
• Increased leak rate
• More frequent repairs and higher costs
• Higher energy bills
• Increased cost per ton produced
• Reduced profits
On the Demand Side
The plant had 21 departments that were major consumers of compressed air. Some of these departments were equipped with vortex flow sensors, but they were not measuring flow accurately. The plant's instrumentation team couldn't remove these sensors for servicing or calibration because they were in-line type, requiring a complete plant shutdown for removal. Additionally, the plant was experiencing leakages of up to 750 CFM. Despite frequent leak repair programs, leaks continued to be a persistent issue. The Pulverized Coal Injection (PCI) process required stable system pressure, and due to the current pressure drops, the loading pressures for all three compressors were set 1 bar higher than the PCI department's requirements.